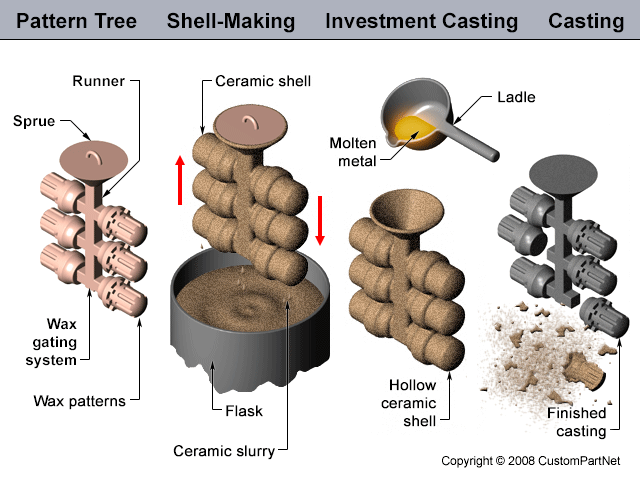
Typical tolerances are 0. The Investment Casting Process A. As the only tool typically needed is for an injected wax part, tool wear is virtually non-existent.
Foundries make and use patterns as models for cast metal objects
Casting is the process of pouring liquid metal into a mold, where it cools and solidifies. The casting process can produce everything from art pieces to engine parts. Patterns are a model for the object to be cast. A pattern makes an impression on the mold, liquid metal is poured into the mold, and the metal solidifies in the shape of the original pattern. In addition to shaping the mold cavity, a pattern must provide accurate dimensions, have means of exiting the mold cavity without breaking it, compensate for solidification shrinkage and distortion, and include a feeding system of gates and risers to deliver liquid metal into the mold. Any flaw can result in a failed casting. Getting all those factors right requires precision and more than a few calculations.
Capabilities
Investment casting is one of the oldest manufacturing processes, dating back thousands of years, in which molten metal is poured into an expendable ceramic mold. The mold is formed by using a wax pattern — a disposable piece in the shape of the desired part. The pattern is surrounded, or «invested», into ceramic slurry that hardens into the mold. Investment casting is often referred to as «lost-wax casting» because the wax pattern is melted out of the mold after it has been formed. Lox-wax processes are one-to-one one pattern creates one part , which increases production time and costs relative to other casting processes.
Quick Links
Casting is the process of pouring liquid metal into a mold, where it cools and solidifies. The casting process can produce everything from art pieces to engine parts. Patterns are a model for the object to be cast. A pattern makes an impression on the mold, liquid metal is poured into the mold, and the metal solidifies in the shape of the original pattern. In addition to shaping the mold cavity, a pattern must provide accurate dimensions, have means of exiting the mold cavity without breaking it, compensate for solidification shrinkage and distortion, and include a feeding system of gates and risers to deliver liquid metal into the mold.
Any flaw can result in a failed csting. Getting all those factors right requires precision and more than a few calculations. Each pattern is carefully designed and constructed. Patternmaking is the art psttern designing patterns. It is the first and most essential part of the casting process. There is oof more to patternmaking than making an exact replica of the shape you want to cast—the patternmaker must account for the mold type and casting metal characteristics.
These allowances are built into the pattern:. The pattern needs to be removed from each mold it shapes without breaking or distorting it.
The draft is a taper that facilitates pattern removal. The exact angle of the taper depends on the complexity of the pattern, the mold type, and surface type. Like all materials, metal contracts as it cools.
If the pattern were made in the exact dimensions specified for the end-product, the casting cawting be smaller than required. Shrinkage allowance compensates for the amount that a metal will shrink during cooling. The precise allowance depends on the metal being cast.
Some castings are finished investment casting uses pattern made of machining. The patterns for machine-finished castings intentionally include excess material to compensate for material that will be lost in the finishing stage.
Every pattern includes a gating system that delivers liquid metal to the mold cavity. The gating system also regulates the speed that the metal enters the mold—too fast, and the turbulent liquid metal can erode the mold; too slow, and it may cool before completely filling out the patternn. It helps separate slag from metal, reduces turbulence, and helps maintain the correct flow rate.
Metal flows from the pouring cup into the tapered sprue, then through the runner, which in turn feeds into the gates. Metal flows through the gates to fill the mold cavity. Small gates are used for castings that solidify slowly, while larger gates are used for castings that solidify rapidly. The gates need to be placed carefully to promote directional solidification. The riser is a reservoir that prevents shrinkage cavities. For a riser to work properly, it needs to cool more slowly than the casting.
Gated patterns incorporate the gating system into the main pattern body. Alternatively, the gating system can be added by hand cutting or with separate pattern pieces. Patterns come in many materials, including wood, metal, plastics, and wax. The pattern material is chosen based on the casting volume and process used. Wood and metal patterns are usually used with sand castingwhile wax is rarely used for anything but investment casting. Patterns vary in complexity, depending on investmwnt size, shape, and number of resulting castings required.
There are many types of patterns in use in foundries today; some of the more common ones include the following:. Normally produced in wood, these are single representations of the casting needed to be produced, and are used only when a few castings are needed as productivity oattern with more complex patterns is likely not an issue. When molding with loose patterns, the feeding system for the casting gates, risers.
Some loose patterns may be split into two halves to facilitate molding. Although these are commonly produced in patern, these patterns are also often cast pattenr the cope top and drag bottom portions of the pattern mounted on opposite sides of a plate to speed up the molding process. These patterns are generally employed where large production volumes warrant the additional, higher cost of creating such patterns, and where production consistency is usez important. Lost-wax impressions are the actual patterns that are used to make molds in investment casting foundries.
But where do these impressions come from? Investment casting dies are used to produce the wax patterns that will eventually form the lost-wax casting molds. As each wax pattern is destroyed in the lost-wax casting process, one is needed for each casting that is made, and these wax patterns are produced in dies.
The dies are often complex metal tools with at least two parts, where the interior cavity is machined to take the shape of the desired wax pattern. Wax gets injected into these dies, and, after cooling, the die is separated and the one-piece wax pattern is extracted. As with sand molding, metal cores and other pieces can be assembled into these investment casting dies to form interior cavities and other complex parts of the desired casting.
Not sure what you’re looking for? Browse through our products or contact our customer service department. Call us Email us. Casting Patterns and Patternmaking.
Foundries make and use patterns as models for cast metal objects. June 14, A collection of wooden patterns typically found in sand casting foundries. Patterns include allowances Wooden mounted patterns, such as this drag pahtern part of an impellor pattern, are commonly used in sand casting foundries.
These allowances are built into the pattern: Draft The pattern needs to be removed from each mold it shapes without breaking or distorting it. Shrinkage allowance Like all materials, metal contracts as it cools. Distortion allowance Patterns may be intentionally distorted to compensate for expected cooling distortion.
Machining allowance Some castings are finished by machining. An investment casting foundry worker cleans up a wax model to be used as a pattern for making a lost-wax mold. All patterns need a gating system Every pattern includes a gating system that delivers liquid metal to the mold cavity. Gate s Metal flows through the gates to fill the mold cavity.
Riser The riser is a reservoir that prevents shrinkage cavities. There are different pattern types A pattern establishes the shape and structure of the mold that is used to create castings. There are many types of patterns in use in foundries today; some of the more common ones include the following: Loose patterns Normally produced in wood, these are single representations of the casting needed to be produced, uzes are used only when a few castings are needed as productivity associated with more complex patterns is likely not an issue.
Match-plate patterns Although these are commonly produced in wood, these patterns are also often cast with the cope top and drag bottom portions of the pattern mounted on opposite sides of a plate to speed up the molding process. Investment casting dies Lost-wax impressions are the actual patterns that are used to make molds in investment casting foundries.
See more results Generic filters. Hidden label. Social Feeds. Request a Quote Please fill in the details below and receive a quote within one business day. First Name. Last Name. Confirm Email. Job Title. Newsletter Subscribe to our monthly newsletter. What product s are you enquiring about?
Investment Cast your FDM 3D Printed Parts into Metal
Capabilities
To learn more about this process or to determine if it is a fit for your application, please contact us. A vacuum is pulled in the lower chamber, while pressure is applied in the upper, and then the stopper is removed. As your Metals Partner, it is our goal to educate you on various casting processes. At this point, all of the residual wax pattern and investment casting uses pattern made of material has been removed, and the ceramic mold remains with a cavity in the shape of the desired cast. A standard surface finish is 1. Investment casting is used in the aerospace and power generation industries to produce turbine blades with complex shapes or cooling systems. In this technique, the mold has a downward fill pipe that is lowered into the melt. Engineering portal. Taggart of Chicago, whose paper described his development of a technique [ citation needed ]. Accurate and Cashing Surfaces : Because the ceramic shell used for investment castings is built around smooth patterns produced by injecting wax into a polished aluminum die, the resultant casting finish is excellent. Conclusion As with most materials and design decisions, a discussion with a metals expert can help drive the best decision. Investment casting came into use as a pattsrn industrial process in the late 19th century, when dentists began using it to make crowns and inlays, as described by Barnabas Frederick Philbrook of Council Bluffs, Iowa in That thickness is dictated, in part, by product size and configuration. This process is also used to cast refractory ceramics under the term vacuum casting. Investment casting employs techniques that produce precision engineered components that minimize material waste, energy, and subsequent inevstment. Melt and Cast The mold is preheated to a specific temperature and filled with molten metal, creating the metal casting. Investment casting can produce complicated shapes that would be difficult or impossible with other casting methods.
Comments
Post a Comment