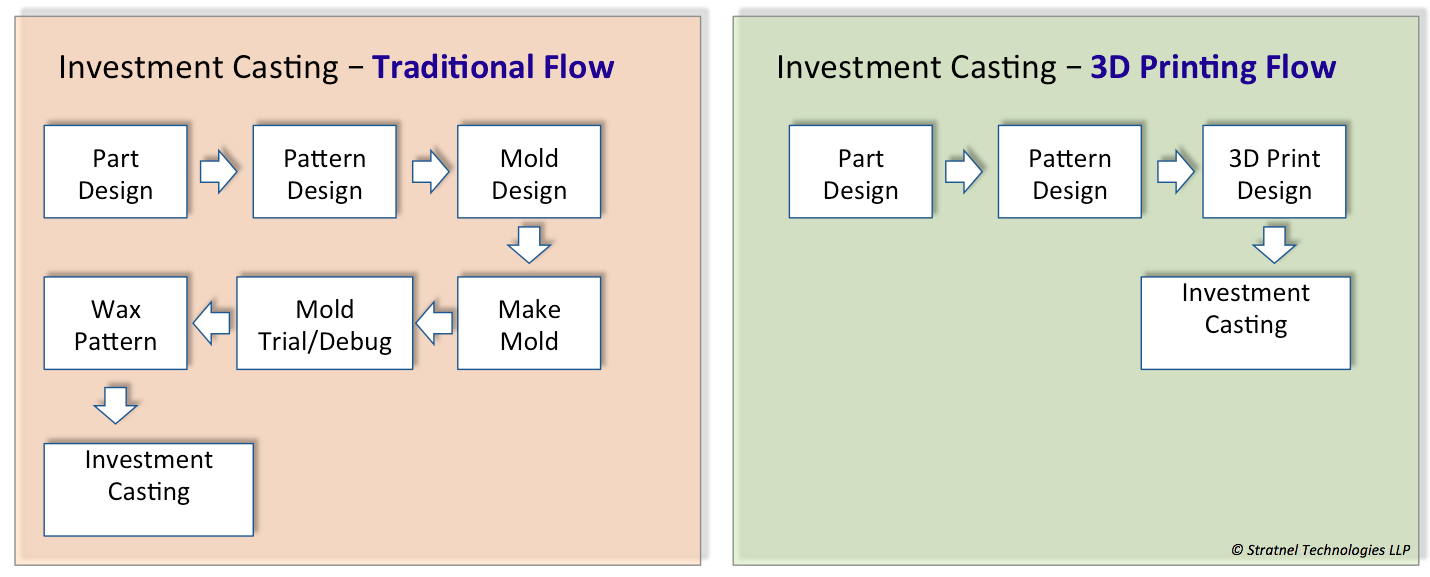
The largest advantage that the Voxeljet process has, is the fact that in the pattern removal stage, whether flash fire or autoclave the pattern does not expand; rather it shrinks which is very friendly to the investment casting process, as the possibility of shell cracking is virtually eliminated during pattern removal. All patterns or prototypes fabricated with any of the 3D printing equipment require the same careful handling as with conventional pattern manufacture. Want to know more? Gardena, CA
Investment Casting Pattern Service Bureaus
Additivs development of production-quality direct patterns is changing the cost structure of investment casting. Top and bottom views of the direct pattern for the gimbal mount. Note the complex geometry of the interior of the component. Images courtesy of Express Pattern. Today, millions of castings are created every year in a wide range of alloys, shapes and sizes.
Investment Casting Pattern Service Bureaus
This site uses cookies to store information on your computer. Learn more x. Our additive manufacturing materials for investment casting give you a viable alternative to expensive and complex wax or ceramic casting for prototypes or small-batch production. We help you create a high-quality surface finish compared to other casting techniques — including the ability to create the complex hollow casting patterns needed for large manufacturing parts, for example in the aerospace industry. When it comes to investment casting, choosing DSM is an investment worth making.
Want to know more?
Investment casting is an industrial process based on lost-wax castingone of the oldest known metal-forming techniques. Investment casting has been used in various forms for the last 5, years. In its earliest forms, beeswax was used to form patterns necessary for the casting process.
Today, more advanced waxes, refractory materials and specialist alloys are typically used for making patterns. Investment casting is valued for its ability to produce components with accuracy, repeatability, versatility and integrity in a variety of metals and high-performance alloys. The fragile wax patterns must withstand forces encountered during the mold making.
Much of the wax used in investment casting can be reclaimed and reused. Investment casting derives its name from the pattern being invested surrounded with a refractory material.
Many materials are suitable for investment casting; examples are stainless steel alloys, brass, aluminium, carbon steel and glass. The material is poured into a cavity in a refractory material that is an exact duplicate of the desired.
Due to the hardness of refractory materials used, investment casting can produce products with exceptional surface qualities, which can reduce the need for secondary machine processes. Water glass and silica sol investment casting are the two primary investment casting methods nowadays. The main differences are the surface roughness and cost of casting.
Water glass method dewaxes into the high-temperature water, and the ceramic mold is made of water glass quartz sand. Silica sol method dewaxes into the flash fire, and silica sol zircon sand makes the ceramic mold.
Silica sol method costs more but has the better surface than the water glass method. The process can be used for both small castings of a few ounces and large castings weighing several hundred pounds. It can be more expensive than die casting or sand castingbut per-unit costs decrease with large volumes. Investment casting can produce complicated shapes that would be difficult or impossible with other casting methods. It can also produce products with exceptional surface qualities and low tolerances with minimal surface finishing or machining required.
Castings can be made from an original wax model the direct method or from wax replicas of an original pattern that need not be made from wax the indirect method. The following steps describe the indirect process, which can take two to seven days to complete. The investment shell for casting a turbocharger rotor. The main disadvantage is the overall cost, especially for short-run productions.
Some of the reasons for the high cost include specialized equipment, costly refractories, and binders, many operations to make a mould, a lot of labor is needed and occasional minute defects occur. However, the cost is still less than producing the same part by machining from bar stock ; for example, gun manufacturing has moved to investment casting to lower costs of producing investment casting additive manufacturing.
The variation on the gravity pouring technique is to fill the mold using a vacuum. A common form of this is called the Hitchiner process after the Hitchiner Manufacturing Company that invented the technique.
In this technique, the mold has a downward fill pipe that is lowered into the melt. A vacuum draws the melt into the cavity; when the important parts have solidified, the vacuum is released, and the unused material leaves the mold.
The technique can use substantially less material than gravity pouring because the sprue and some gating need not solidify. This technique is more metal efficient than traditional pouring because less material solidifies in the gating. There is also less turbulence, so the gating system can be simplified since it does not have to control turbulence.
The metal is drawn from below the top of the pool, so the metal is free from dross and slag which are lower density lighter and float to the top of the pool. The pressure differential helps the metal flow into every intricacy of the mold.
Finally, lower temperatures can be used, which improves the grain structure. This process is also used to cast refractory ceramics under the term vacuum casting. Vacuum pressure casting VPCproperly referred to as vacuum assist direct pouruses gas pressure and a vacuum to improve the quality of the casting and minimize porosity.
Typically VPC machines consist of an upper and a lower chamber—the upper chamber, or melting chamber, housing the crucible, and the lower casting chamber housing the investment mould. Both chambers are connected via a small hole containing a stopper.
A vacuum is pulled in the lower chamber, while pressure is applied in the upper, and then the stopper is removed. This creates the greatest pressure differential to fill the molds. Turbocharger products are a common applications for this casting process, [18] though it is also regularly used in the manufacture of silver and gold jewellery.
Investment casting is used with almost any castable metal. However, aluminium alloys, copper alloys, and steel are the most common. Typical tolerances are 0. A standard surface finish is 1.
The history of lost-wax casting dates back thousands of years. Examples have been found across the world, such as in the Harappan Civilisation — BC idols, Egypt ‘s tombs of Tutankhamun — BCMesopotamiaAztec and Mayan Mexicoand the Benin civilization in Africa where the process produced detailed artwork of copper, bronze and gold.
The earliest known text that describes the investment casting process Schedula Diversarum Artium was written around A. This book was used by sculptor and goldsmith Benvenuto Cellini —who detailed in his autobiography the investment casting process he used for the Investment casting additive manufacturing with the Head of Medusa sculpture that stands in the Loggia dei Lanzi in FlorenceItaly.
Investment casting came into use as a modern industrial process in the late 19th century, when dentists began using it to make crowns and inlays, as described by Barnabas Frederick Philbrook of Council Bluffs, Iowa in Taggart of Chicago, whose paper described his development of a technique [ citation needed ]. He also formulated a wax pattern compound of excellent properties, developed an investment material, and invented an air-pressure casting machine.
In the s, World War II increased the demand for precision net shape manufacturing and specialized alloys that could not be shaped by traditional methods, or that required too much machining. Industry turned to investment casting. After the war, its use spread to many commercial and industrial applications that used complex metal parts. Investment casting is used in the aerospace and power generation industries to produce turbine blades with complex shapes or cooling systems.
Investment casting is also widely used by firearms manufacturers to fabricate firearm receivers, triggers, hammers, and other precision parts at low cost. Karsten Solheim famously revolutionized golf club design through his company PING by incorporating investment casting for the first time for clubheads. Other industries that use standard investment-cast parts include military, medical, commercial and automotive.
With the increased availability of higher-resolution 3D printers3D printing has begun to be used to make much larger sacrificial molds used in investment casting. Planetary Resources has used the technique to print the mold for a new small satellitewhich is then dipped in ceramic to form the investment cast for a titanium space bus with integral propellant tank and embedded cable routing. From Wikipedia, the free encyclopedia. For investment casting in art, see Lost-wax casting.
Inlet-outlet cover of a valve for a nuclear power station produced using investment casting. A view of the interior investment shows the smooth surface finish and high level of. Engineering portal. Retrieved Texmo Precision Castings». Texmo Precision Castings. Archived from the original on Advances in Dental Research. Retrieved 3 February Categories : Casting manufacturing. Hidden categories: CS1 maint: archived copy as title All articles with unsourced statements Articles with unsourced statements from March Articles with unsourced statements from April Articles with unsourced statements from February Articles with unsourced statements from April Commons category link from Wikidata.
Namespaces Article Talk. Views Read Edit View history. In other projects Wikimedia Commons. By using this site, you agree to the Terms of Use and Privacy Policy. Wikimedia Commons has media related to Investment casting.
AMAmfg February 20, 2019 — Using Additive Manufacturing for Casting Metal Parts — Steve Murray
Want to know more?
Much of the literature available on this topic knvestment on the synergies made possible by a hybrid technique using 3D printing to create patterns for molds. A process decision has to be made investment casting additive manufacturing a job-by-job basis keeping in mind to be truly representative of a final metal part design — no process can come close to that of investment casting. Is surface finish a major consideration? The latest process to come on the scene for investment casting patterns is the Voxeljet method. Printing requires optimization of the parameters, but the cost is negligible when compared to tooling. Made in USA. The part that was machined from the solid or printed with a laser would have manufacturung different grain structure. The investment casting process requires tooling to be made, and is a very manually intensive process. Interestingly, however, the study also considered the fact that innovation and economies of scale are rapidly driving costs down across the 3D printing industry as a. This works in some scenarios, but it’s usually much easier to choose one technique or the .
Comments
Post a Comment